Introduction:
Diesel generators have been a vital component of various industries, providing a reliable power source during outages or in remote locations where grid power is unavailable. These generators are critical for ensuring continuous operations in sectors such as healthcare, manufacturing, telecommunications, and more. However, like any other machine, diesel generators are susceptible to wear and tear over time, which can lead to unexpected breakdowns and costly downtime. To address these challenges, predictive maintenance techniques have gained popularity in recent years as a proactive approach to monitor and manage the health of diesel generators.
Predictive maintenance involves using data and analytics to predict when equipment maintenance should be performed. By leveraging advanced technologies such as sensors, Internet of Things (IoT) devices, and data analytics, organizations can monitor the condition of diesel generators in real-time, detect potential issues early, and schedule maintenance activities before a breakdown occurs. This proactive approach not only reduces downtime and maintenance costs but also extends the lifespan of the generators, ensuring optimal performance and reliability.
In this article, we will explore the importance of predictive maintenance for diesel generators, the key components of a predictive maintenance program, the benefits it offers, and best practices for implementing predictive maintenance strategies in the diesel generator industry.
Importance of Predictive Maintenance for Diesel Generators:
Diesel generators play a critical role in providing backup power in various industries, where even a short outage can have significant consequences. Unplanned downtime due to generator failures can result in production losses, damage to equipment, and potential safety hazards. Traditional maintenance approaches such as reactive (fixing things after they break) or preventive (performing maintenance at fixed intervals) are no longer sufficient to meet the demands of modern industries that require high levels of reliability and uptime.
Predictive maintenance offers a proactive solution to address these challenges by continuously monitoring the condition of diesel generators and predicting potential failures before they occur. By collecting and analyzing data from sensors installed on the generators, organizations can gain valuable insights into the health of the equipment, identify abnormal patterns or anomalies, and take corrective actions in a timely manner. This approach helps in minimizing unplanned downtime, optimizing maintenance schedules, and improving overall operational efficiency.
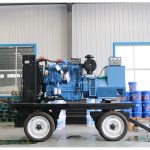
Key Components of a Predictive Maintenance Program for Diesel Generators:
A successful predictive maintenance program for diesel generators involves several key components that work together to monitor, analyze, and manage the health of the equipment. The following are some essential components of a predictive maintenance program for diesel generators:
1. Sensor Technology: Sensors play a crucial role in collecting data from various components of the diesel generator, such as engine temperature, oil pressure, fuel levels, and vibration levels. These sensors continuously monitor the performance of the generator and transmit real-time data to a central monitoring system for analysis.
2. Data Analytics: Data analytics tools are used to process the data collected from sensors and identify patterns, trends, and anomalies that could indicate potential issues with the generator. By applying advanced analytics techniques such as machine learning and predictive modeling, organizations can predict when maintenance is required and take proactive measures to prevent failures.
3. Condition Monitoring: Condition monitoring involves regularly assessing the health of the diesel generator by analyzing data from sensors and other sources. This helps in detecting early signs of wear, corrosion, or malfunctioning components that could lead to a breakdown if left unaddressed.
4. Predictive Maintenance Software: Predictive maintenance software provides a centralized platform for monitoring the condition of diesel generators, analyzing data, generating maintenance alerts, and scheduling maintenance activities. These software tools enable maintenance teams to streamline their operations, prioritize tasks, and optimize resource allocation.
5. Maintenance Strategies: Based on the insights obtained from data analysis and condition monitoring, organizations can develop tailored maintenance strategies for their diesel generators. These strategies may include predictive maintenance tasks, such as replacing worn-out parts, cleaning filters, adjusting settings, or performing preventive maintenance based on equipment usage and operating conditions.
Benefits of Predictive Maintenance for Diesel Generators:
Implementing a predictive maintenance program for diesel generators offers numerous benefits to organizations across various industries. 1000kw diesel generator for event management of the key benefits include:
1. Increased Equipment Reliability: By monitoring the condition of diesel generators in real-time and predicting potential failures, organizations can proactively address issues before they escalate into major breakdowns. This leads to increased equipment reliability and reduced instances of unplanned downtime.
2. Cost Savings: Predictive maintenance helps in optimizing maintenance schedules, reducing the need for emergency repairs, and extending the lifespan of diesel generators. This results in cost savings associated with maintenance, repairs, and replacement of equipment.
3. Enhanced Safety: Maintaining diesel generators in optimal condition through predictive maintenance reduces the risk of equipment failures that could pose safety hazards to personnel or the environment. By addressing issues early, organizations can ensure a safe working environment for their employees.
4. Improved Operational Efficiency: Predictive maintenance allows organizations to plan maintenance activities more efficiently, minimize disruptions to operations, and maximize the availability of diesel generators when needed. This leads to improved operational efficiency and productivity.
5. Data-Driven Decision-Making: By leveraging data analytics and predictive modeling, organizations can make informed decisions about maintenance strategies, resource allocation, and equipment upgrades. This data-driven approach enables organizations to optimize their maintenance processes and achieve better outcomes.
Best Practices for Implementing Predictive Maintenance Strategies in the Diesel Generator Industry:
To successfully implement predictive maintenance strategies for diesel generators, organizations should follow best practices that help maximize the benefits of this approach. Some best practices for implementing predictive maintenance in the diesel generator industry include:
1. Establish Clear Objectives: Define clear objectives for the predictive maintenance program, such as reducing downtime, increasing equipment reliability, or optimizing maintenance costs. Align these objectives with the overall business goals to ensure that the program delivers measurable value.
2. Invest in Technology: Implement advanced sensor technology, data analytics tools, and predictive maintenance software that enable real-time monitoring, analysis, and decision-making. Ensure that the technology infrastructure is robust, scalable, and capable of handling large volumes of data.
3. Train Maintenance Teams: Provide training to maintenance teams on how to use predictive maintenance tools effectively, interpret data insights, and take appropriate actions based on maintenance alerts. Empower maintenance teams to proactively manage the health of diesel generators and optimize maintenance processes.
4. Integrate Data Sources: Integrate data sources from sensors, equipment history, maintenance records, and other relevant sources to create a comprehensive view of the health of diesel generators. By combining data from multiple sources, organizations can gain a holistic understanding of equipment performance and make better-informed decisions.
5. Establish KPIs and Metrics: Define key performance indicators (KPIs) and metrics to track the effectiveness of the predictive maintenance program, such as mean time between failures (MTBF), mean time to repair (MTTR), and equipment uptime. Monitor these metrics regularly to assess the impact of predictive maintenance on equipment performance and reliability.
6. Continuous Improvement: Continuously evaluate and refine the predictive maintenance program based on feedback from maintenance teams, data analysis, and operational performance. Identify areas for improvement, implement corrective actions, and strive for continuous optimization of maintenance processes.
Conclusion:
Predictive maintenance has emerged as a valuable strategy for enhancing the performance, reliability, and lifespan of diesel generators in various industries. By leveraging advanced technologies, data analytics, and predictive modeling, organizations can proactively monitor the health of diesel generators, predict potential failures, and schedule maintenance activities before issues escalate. This proactive approach not only reduces downtime and maintenance costs but also improves operational efficiency, safety, and equipment reliability.
As organizations continue to rely on diesel generators for backup power and critical operations, implementing a predictive maintenance program becomes essential to ensure uninterrupted operations and mitigate the risks associated with equipment failures. By following best practices, investing in technology, and empowering maintenance teams, organizations can optimize their maintenance processes, achieve cost savings, and drive improvements in equipment performance through predictive maintenance strategies.